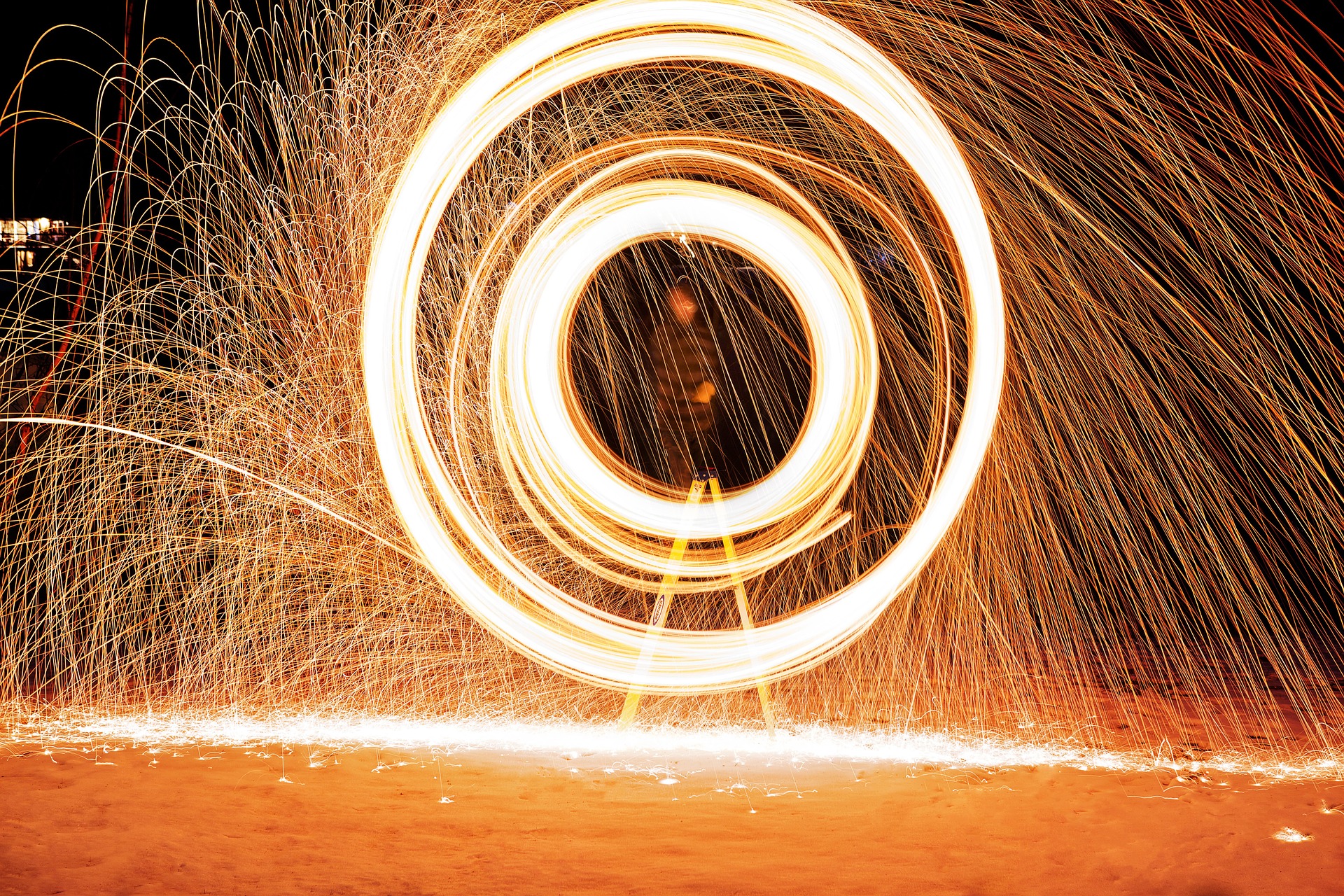
Fusion software to optimize mirrors for EUV lithography
A software code to optimize holographic diffraction grating for a fusion plasma diagnosis spectrometer
Developed at the Forschungszentrum Jülich and used to develop diffraction gratings for “HEXOS” the Plasma diagnostic spectrometer for Wendelstein 7-X (W7-X), this software code determines manufacturing parameters for an optimized holographic diffraction grating on a concave or toroidal surface, together with the geometry of the corresponding VUV spectrometer arrangement (entrance slit, grating and detector). Originally, the technology was used to develop VUV spectrometers for fusion tokamaks.
Accurate gratings providing sharp spectro-metric images at high efficiency and low stray light level. These results could not be achieved by mechanically ruled gratings or by holographic gratings on flat surfaces.
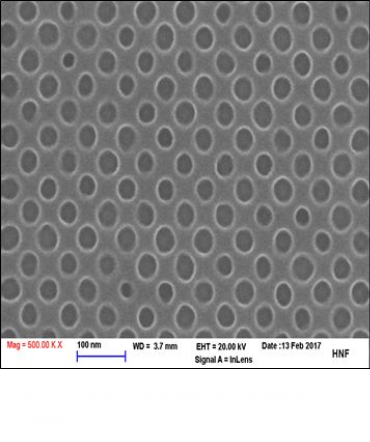
28nm HP contact holes printed with interference exposer EUV-LET
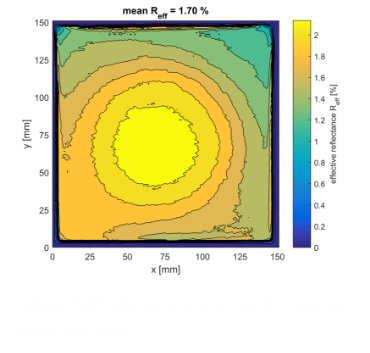
Full area AIMER effective reflectance map of an absorber coated mask blank
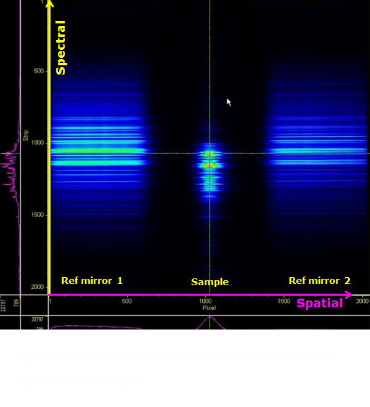
Spectral resolved EUV from mask (center) compared to ref mirrors (left/right)
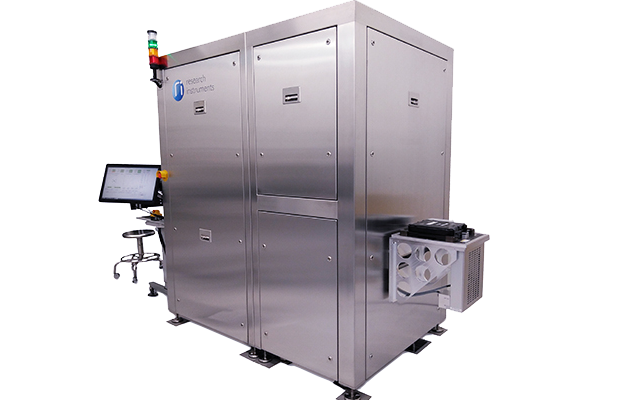
EUV mask blank reflectometer
Improving mirrors for EUV lithography
The transfer project was initiated by a request from Dr Rainer Lebert of AIXUV (Aachen, Germany) to Professor Wolfgang Biel for the calculation of a diffraction grating to be used as the central optical component in an EUV reflectometer (apparatus for measuring the absolute reflectivity of multilayer mirrors in the 13 nm range). The initial objective is the qualification and improvement of mirrors for EUV lithography (chip fabrication) that allow high precision measurement. With the increasing importance of mass production of chips by EUV lithography (EUVL), there is indeed a real need for actinic EUV solutions at the 13.5 nm lithography wavelength, metrology and tools for research, development and supply chain quality control.
Following the takeover of AIXUV by Bruker, the technology was transferred to Research Instruments (RI, Bergisch-Gladbach). Research Instruments (RI) develops and manufactures high-performance components, and systems, and provides solutions for scientific and industrial applications, and customers around the globe. The company is renowned for providing most reliable services and products ranging from prototypes and custom-tailored components, to series production and turn-key systems. It complements high-level mechanical, electrical and control systems engineering with RF and pulsed power technology, and a unique infrastructure allowing for on-site high-precision machining, welding and brazing processes, chemical surface preparation, physical coating, clean room assembly, electrical manufacturing, and state-of-the-art test facilities. RI has set standards for building particle accelerators, equipment for photon instrumentation and EUV metrology, and products for fusion technology, healthcare and industry.