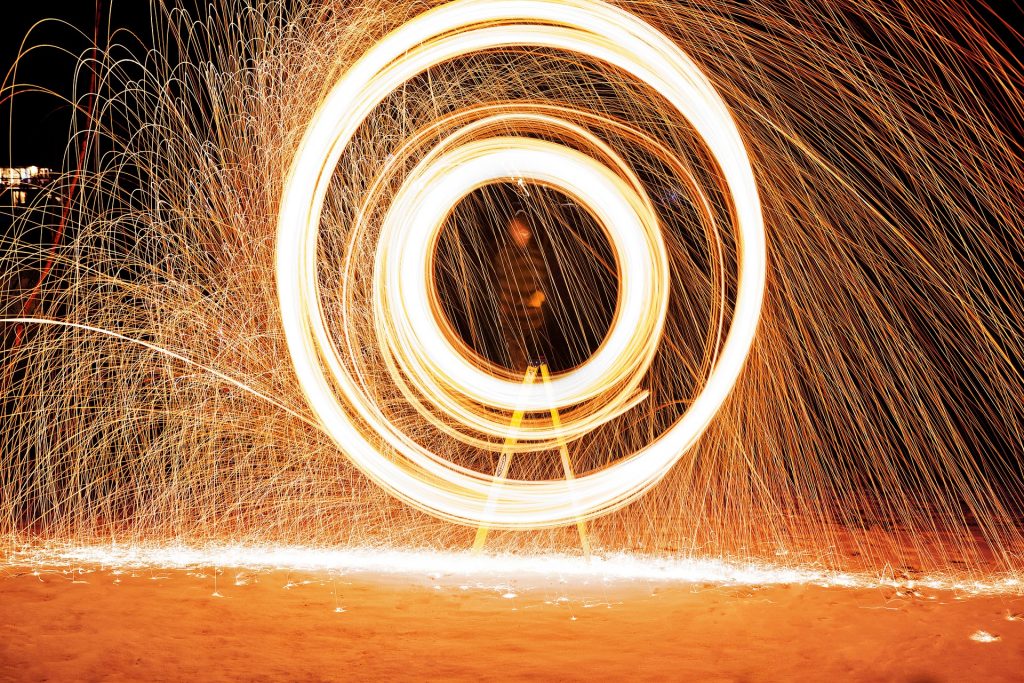
Sourcing new fusion technologies everywhere in Europe to foster your innovation…
Abstract
The present offer describes an additive manufacturing (AM) technology for tungsten which is a refractory metal with outstanding properties as tungsten exhibits e.g. the highest melting point as well as the lowest vapour pressure of all metals. With such a manufacturing approach, geometrically complex tungsten parts can be realised straightforwardly which means that fabrication flexibilities beyond the possibilities of conventional manufacturing methods are provided. The AM of tungsten can be of interest regarding various applications for which complexly shaped tungsten parts are required or desirable. The development work regarding the AM method described within the present offer was during recent years being performed by R&D institutions for plasma facing materials in fusion.
Description of the Technology
Tungsten is a refractory metal with outstanding properties. It for example exhibits the highest melting point as well as the lowest vapour pressure of all metals. Due to such exceptional properties, tungsten and tungsten based alloys are typically used with respect to demanding high temperature and high heat flux applications. From an engineering point of view, however, tungsten is a challenging material to work with as it is an inherently hard and brittle metal.
Established fabrication and machining technologies for tungsten are hence a limiting factor regarding the design and realisation of tungsten components. Against these limitations, AM methods could represent a versatile approach for the realisation of geometrically complex tungsten parts. AM is a term that describes manufacturing processes in which three-dimensional objects are created by means of sequential deposition of layers under computer control. Such processes offer advantages in comparison with conventional manufacturing technologies as parts with high geometrical complexity can be realised straightforwardly.
In recent years, substantial progress has been achieved regarding the AM of metals by means of laser powder bed fusion (LPBF) which is a technology that allows the direct AM of metals without the need for binder phases. In this context, a LPBF process was elaborated for the additive fabrication of tungsten parts which might be of interest with respect to various applications for which geometrically complex tungsten or refractory metal parts are required or desirable.
Innovation and advantages of the offer
Tungsten is a particularly challenging material for LPBF processing due to the intrinsic properties of this metal, especially the high ductile-to-brittle transition temperature, in combination with the high thermal gradients that occur during a LPBF process due to the laser-material interaction. Hence, tungsten parts fabricated by means of LPBF typically exhibit microcracks that manifest during metallographic investigations. Up to now, several studies confirm this microcrack formation but there is currently no method known that completely mitigates microcracks in tungsten consolidated by means of LPBF. The AM process described within this offer may prove innovative and useful as it offers flexibilities beyond the possibilities that conventional manufacturing and machining methods regarding tungsten products provide..
Non fusion applications
The AM of tungsten can be of interest regarding various applications for which complexly shaped tungsten or refractory metal parts are required or desirable. This might e.g. include high temperature or shielding applications.
EUROfusion Heritage
The preferred plasma-facing material in present-day and future magnetic confinement thermonuclear fusion devices is tungsten. This material is mainly chosen because of its high threshold energy for sputtering by hydrogen isotopes as well as its low retention of tritium within the material. From an engineering point of view, however, tungsten is a challenging material to work with as it is an inherently hard and brittle metal. In this respect, established fabrication technologies for tungsten and tungsten based materials are a limiting factor directly affecting the design of plasma-facing components. Against this background, AM technologies for tungsten are being investigated as they could prove very beneficial with regard to plasma-facing component applications due the fact that they offer flexibilities beyond the possibilities that conventional manufacturing methods offer. Development work regarding the LPBF of tungsten was pursued during recent years in the context of the EUROfusion power plant physics and technology (PPPT) work packages materials (MAT) and divertor (DIV) since 2016.