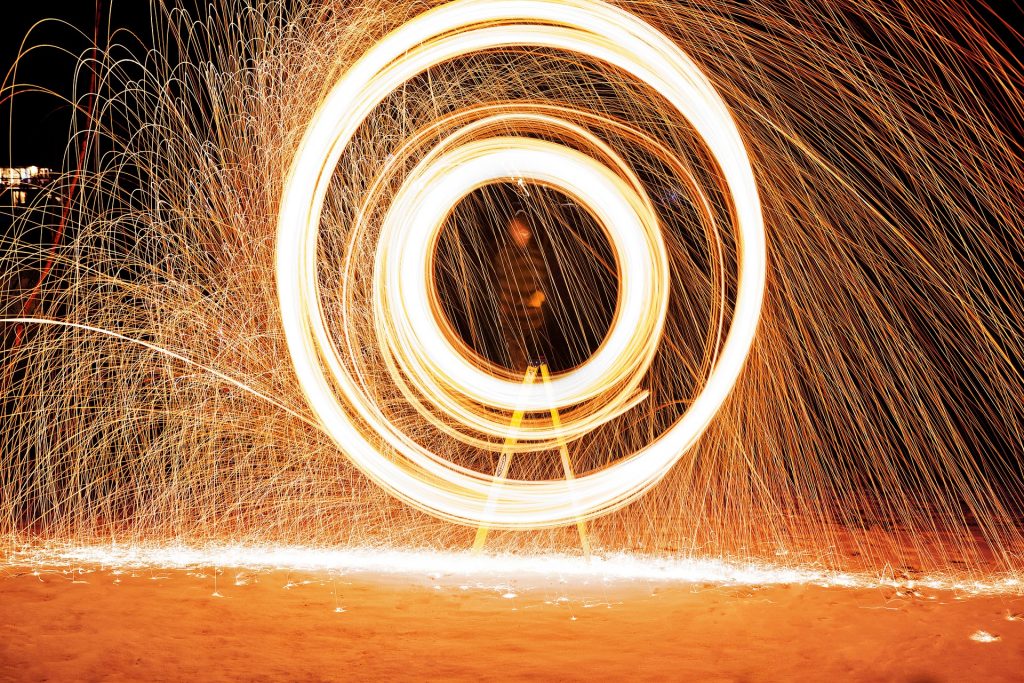
Sourcing new fusion technologies everywhere in Europe to foster your innovation…
Abstract
Developed at KIT (Karlsruhe Institute of Technology) for Test-Blanket-Module components, this technology offers increases limits in length/diameter ratio and precision (drift) of pilot holes used for Electrical Discharge Machining (wire cutting). Instead of fabricating a start hole e.g. by deep-hole drilling, grooves are machined into the surface of bodies by standard machining. The bodies are then joined together using diffusion welding. Thus, limits in terms of length/diameter ration as well as drift along the drill axis can be eliminated. This fusion based technology and know-how could now find promising applications in the field of hard metal processing companies and EDM equipment manufacturers.
Description of the Technology
The technology has been developed to overcome limits in pilot hole fabrication using EDM (wire cutting). Nuclear fusion components, e.g. the First Wall are penetrated by cooling channels, one option for fabrication is EDM. Typical length/diameter ratios in this application are in the order of 200 and thus close to (or even beyond) technological limits with regard to precision requirements (drifting) in terms of deep-hole drilling.
The technology described here was developed in order to increase limits in length/diameter ratio and precision (drift) of pilot holes used for Electrical Discharge Machining (wire cutting). Instead of fabricating a start hole e.g. by deep-hole drilling, grooves are machined into the surface of bodies by standard machining. The bodies are then joined together using diffusion welding. Thus, limits in terms of length/diameter ration as well as drift along the drill axis can be eliminated. Length/diameter-rations > 250 are reachable (e.g. channel diameter 2 mm, length = 1000 mm is possible). KIT has also a strong expertise behind the technology offer: innovative and flexible combination and application of multiple manufacturing processes (EDM, forming, Additive Manufacturing) and welding technologies.
Innovation and advantages of the offer
The main innovation is to machine grooves into accessible surfaces of segments instead of drilling through a solid body. The surfaces are joined subsequently using Diffusion welding (Hot Isostatic Pressing). The precision limit in using this process routine is driven by standard machining tolerances since the surface is directly accessible while performing the tolerance-sensitive machining operation. Drifting of a drilling device during penetration of a solid is not applicable. To apply the joining operation, the machined grooves are aligned along each other that continuous cavities along the bonding surfaces are formed. Joining is performed in two steps: first by circumferential Electron Beam Welding inside of a vacuum chamber, subsequently inside a HIP -welding chamber at high pressure and temperature to create one solid body with internal penetrations.
Non fusion applications
This fusion based technology and know-how could now find promising applications in the field of hard metal processing companies and EDM equipment manufacturers. Two examples of technologies from aircraft turbine combustion chamber manufacturing to circumvent length limits of cooling channels triggered by pilot hole manufacturing : Shorter segments (~ 300 mm channel length) assembled by EB-welding. Disadvantage: fusion welding seam crossing channels, Fabricate channels directly into a plate without pilot hole by cutting an entry slot directly into the outer surface with the cutting wire. Then manufacture channel and exit via the entry slot. The slot at the external side of the plate is closed subsequently, e.g. by soldering of welding.
EUROfusion Heritage
The technology has been developed at KIT (Karlsruhe Institute of Technology is a technical university of the state of Baden-Württemberg and a national research centre in the Helmholtz-Gemeinschaft) during the nationally funded project BMBF-Förderkennzeichen 03FUS0011: Test-Blanket-Module for ITER: Development and qualification of industrial manufacturing technologies.
Hello! Just wanted to say great site. Continue with the good work!
keep up the great work , I read few posts on this website and I believe that your weblog is real interesting and holds bands of excellent information.
Have you noticed the news has changed its approach recently? Now it seems that it is discussed thoroughly and more in depth. Frankly it is about time we see a change.
I am so happy I found your blog and I absolutely love your information about process for pilot hole fabrication in wire cutting electrical discharge machining edm to improve length diameter ratio and precision! I liked and it is wonderful to know about so many things that are useful for all of us! Thanks a lot for this amazing blog!!
I’ll put her on blue monster energy drink nutrition facts A: I feel good going into the regular season. I had a lot of opportunities with being in a nine-play drive for my first game of the preseason. I did not feel any pain blocking or running routes. I am confident going into Pittsburgh with only one preseason game under my belt.
I got a lump in my throat when I thought of that.
Gdyby zycie bylo sprawiedliwe Elvis by zyl, a wszystkie jego sobowtory bylyby martwe. – Johnny Carson
The way you write make it truly straightforward to read. And the design you use, wow. It truly is a really good combination. And I am wondering whats the name of the template you use?
Istnieja tylko dwa sposoby na zycie – zyc tak jakby nic nie bylo cudem lub tak jakby cudem bylo wszystko. – Albert Einstein
Muchas gracias. ?Como puedo iniciar sesion?
Hey, I think your really on track with this, I cant say I am completely on the same page, but its not really that big of a issue. http://www.piano.m106.com
Your home is valueble for me. Thanks!?This website is mostly a stroll-via for the entire info you wanted about this and didn’t know who to ask. Glimpse here, and you’ll undoubtedly discover it. Free Japan
Jezeli ludzie szepcza i knuja za twoimi plecami to tylko znaczy ze ich wyprzedziles…
Great points. I used to spend alot of my time boating and being involved in sports. It was most certainly the best period of my past and your article kind of brought back me of that. Thanks
Gdy ktos robi Ci kazanie, wysluchaj, usmiechnij sie, skiń glowa, a potem podazaj wlasna droga. Jesli nie zyjesz po swojemu, to tak jakbys nie zyl wcale.
Gwiazdor to człowiek, który latami pracuje jak opętany, by zyskać popularność, a potem zakłada polaryzacyjne okulary, żeby go nie rozpoznano… :-).
Wszyscy umrzemy. Celem nie jest zyc wiecznie, celem jest stworzyc cos, co bedzie zylo. – Chuck Palahniuk
Many thanks for the top notch information and facts covered throughout your website, what follows is a trivial quiz for your blog site readers. Exactly who said the following quote? . . . .Speak softly and carry a big stick; you will go far. Have you considered promoting your blog? add it to SEO Directory right now 🙂 http://www.links.m106.com
Szczescie, ktore posiadasz jest jak ziarno; szczescie, ktore dzielisz – to kwiat. Super Blog 🙂 zapraszam do siebie… http://www.xmc.pl
I just stumbled across your website from a friend’s digg profile. Bless him. Websites like yours are really rare in a webspace full of crap and spam.
Pretty good post. I just stumbled upon your web publication and wanted to say that I have in reality enjoyed reading your blog posts. Any way I’ll be subscribing to your feed and I hope you post again soon.
I really enjoy this template youve got going on on your web page. What is the name of the theme by the way? I was thinking of using this style for the web site I am going to build for my class room project.
This is my first visit to this blog. I am thinking about starting a brand new blog in the same category. Your site gave me some ideas to work with. (Dont worry, I wont be copying you :)) You have done a fantastic job.
We wanted to share with you the best way impressed I’m in your service and product. I really wanted one to know that am almost certainly going to order extra of my own stuff via you due to their low fee in freight along with the speedy shipping and delivery. Just wanted to tell someone the event I just simply had onto your site. My newbie and ?t had been so effortless. Everything was now and quite a confusion. Free WebWebmaster
How one can extend the range of the Wireless N router? Concerning an Xtreme N cellular router (Dlink). I ought to extend the reach from the wireless signal. I have learned to do it for the G signal. I have to know how to do this for an N signal. Is it possible to apply regular N routers as repeaters. If so, how do you configure them. Thanks for any information.
Just desire to say your article is as astonishing. The clearness in your post is simply excellent and i can assume you’re an expert on this subject. Fine with your permission let me to grab your feed to keep updated with forthcoming post. Thanks a million and please keep up the enjoyable work.
Great post! Are there any pespectives that you may be able to divulge in order to justify your last part a small amount further? thanks a lot
Nice site, looks very organized. Finally found what Ive been looking for, thanks!
I was just looking for this information for quite a while. Almost one and a half hours of continuous surfing, luckily I saw that in your blog. I dont understand why Bing never display this sort of good websites in the first page. Usually the top web sites are full of junks. Perhaps it is time to use other search engine.
If Apple did not invent computers and Starbucks didnt invent coffee drinks, precisely why had they become so productive? The journey to offer the most up-to-date and more challenging products, though highly intoxicating, is often a somewhat jampacked line of business. Preferably, Apple and Starbucks built their own niche.
hello anyone, I was just checkin out this blog and I really admire the basis of the article, and have nothing to do, so if anyone would like to to have an interesting conversation about it, please contact me on AIM, my name is rick smith
Hello this post is nice and interesting. I’ll use it for my project . Can you say to me some related articles that I can read too? –
I wish to show my thanks to the writer for rescuing me from this challenge. As a result of surfing through the the web and getting notions which are not helpful, I figured my entire life was gone. Living devoid of the approaches to the problems you have sorted out all through your good post is a critical case, and ones that might have in a wrong way affected my entire career if I hadnt come across your site. Your own knowledge and kindness in controlling every item was tremendous. Im not sure what I would have done if I hadnt encountered such a point like this. Im able to at this time look ahead to my future. Thanks very much for this high quality and results-oriented guide. I will not hesitate to suggest your web site to anyone who will need tips about this matter.
you have a great blog here! would you like to make some invite posts on my blog?
Saved as a favorite, I really like your blog!
Hello, this can be a great blog. Im perpetually on the lookout for websites similar to this. Keep up the nice effort!
Hey 🙂 Just between, are some totally uncorelated websites blogs to ours, however, they are ultimate worth checking out. Super! Great this typography carry on as usual We love Google 🙂
Thank you for the post on your blog. Do you provide an RSS feed?
Starting a site kind of like this one forced me to do some research and I found your post to be quite helpful. My content is centered around the idea of knowledge, fun and sharing. I wish you first-rate luck with your site in the future and you can be sure I’ll be following it.
Im not sure why but this weblog is loading incredibly slow for me. Is anyone else having this problem or is it a issue on my end? Ill check back later on and see if the problem still exists.
Thnkx so much for this! I havent been this moved by a blog for a long time! You have got it, whatever that means in blogging. Well, You are definitely somebody that has something to say that people should hear. Keep up the wonderful work. Keep on inspiring the people!
Hey 🙂 Just between, are some totally uncorelated websites blogs to ours, however, they are ultimate worth checking out. Super! Great this typography carry on as usual
Depending on yourself to make the decisions can really be upsetting and frustrating. Many of us develop this ability over the course of our life. It doesnt really just happen if you know what I mean.
Hi, i read your weblog sometimes and that i own a similar one and i used to be just wondering when you get loads of spam feedback? In that case how do you stop it, any plugin or anything youll be able to recommend? Im getting a lot recently it is driving me mad so any assist could be very much appreciated. Anyway, in my language, there are usually not a lot good supply like this.
Thank you for the post on your blog. Do you provide an RSS feed?
I wanted to check up and allow you to know how , a great deal I cherished discovering this blog today. We would consider it a honor to work at my company and be able to make real use of the tips contributed on your blog and also participate in visitors remarks like this. Should a position regarding guest author become available at your end, remember to let me know.
You are my inspiration , I own few blogs and often run out from to post .
This waspretty beneficial material. Without a dobut I think this is well worth a bookmark, thanks
These kind of post are always inspiring and I prefer to read quality content so I happy to find many good point here in the post, writing is simply great, thank you for the post
Uważaj, żebyś przez nieuwagę nie stworzył czegoś wiekopomnego i na stałe wpisał się w cyfrowy świat internetu. 🙂
Ten wpis robi wielkie wrażenie, swooją lekkością wprawia w osłupienie, Chciałbym tak Jak ty frazować piękne zdania przyjmij najszczersze gesty wielkiego uznania.
Very well written information. It will be helpful to everyone who employess it, as well as myself. Keep up the good work canr wait to read more posts.
ivermectin 3 http://stromectolabc.com/
ivermectin 6mg dosage
ivermectin oral solution http://stromectolabc.com/
ivermectin new zealand
buy ivermectin cream http://stromectolabc.com/
stromectol buy
ivermectin stromectol http://stromectolabc.com/
ivermectin pills
ivermectin price http://stromectolabc.com/
ivermectin generic
zithromax online pharmacy canada https://azithromycin1st.com/
zithromax z-pak price without insurance
zithromax online paypal https://azithromycin1st.com/
zithromax 500mg over the counter
zithromax online zithromax 500mg over the counter zithromax cost australia
purchase zithromax online
buy cheap zithromax online zithromax 250 mg zithromax over the counter uk
zithromax 500
zithromax cost canada zithromax online paypal order zithromax over the counter
zithromax antibiotic without prescription
zithromax 250 mg zithromax 500 mg for sale zithromax online paypal
zithromax for sale 500 mg
zithromax over the counter canada where to get zithromax over the counter how to get zithromax online
can you buy zithromax over the counter in australia
ing. I recently founda reallyinteresting pdf finder type site, its a pdf search engine and I think it is very interesting for people who like reading pdfs
cost of molnupiravir cheap molnupiravir buy molnupiravir online
ivermectin 4 tablets price https://stromectolis.com/
buy ivermectin canada https://stromectolis.com/
ivermectin usa price https://stromectolis.com/
ivermectin purchase https://stromectolis.com/
ivermectin 4 https://stromectolis.com/
purchase stromectol online https://stromectolis.com/
price of ivermectin https://stromectolis.com/
buy stromectol online https://stromectolis.com/
ivermectin 500mg
clomid price cost of clomid clomid alcohol
clomid capsules 50mg