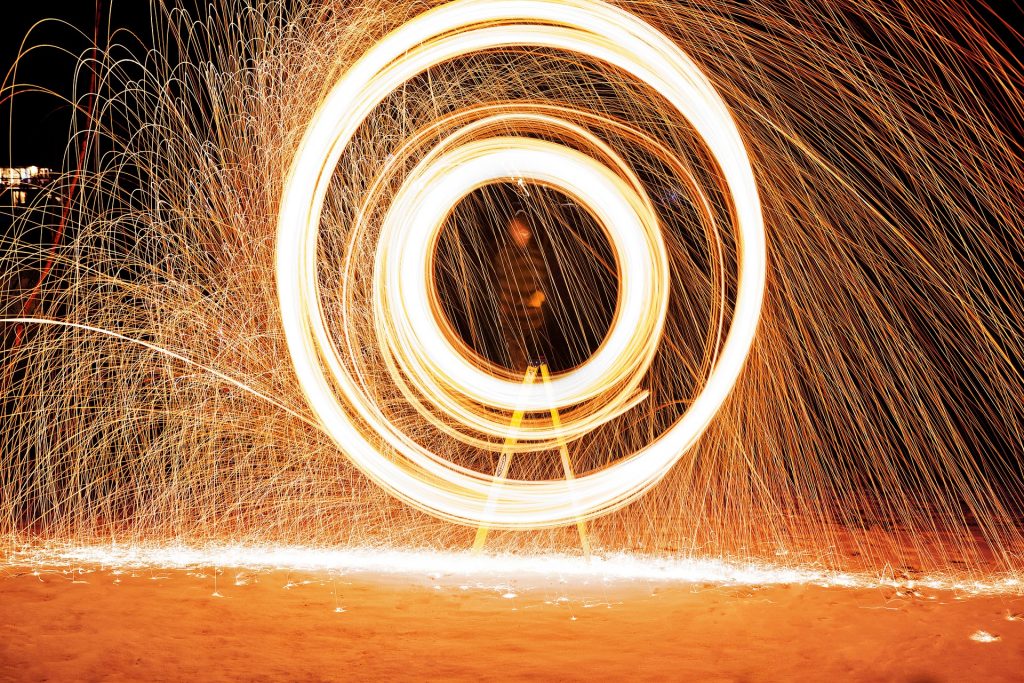
Sourcing new fusion technologies everywhere in Europe to foster your innovation…
Abstract
Materials with high performance regarding thermal properties as well as mechanical properties are required for application in high heat-flux environments, especially in new technologies for advanced energy production such as plasma facing materials in fusion reactors. With the incorporation of high strength and ductile W wire in a W matrix, new tungsten composites can show significantly increased mechanical properties and develop so-called pseudo-ductile behaviour. This new technology could also find promising applications in areas such as high temperature x-ray cathodes, concentrated solar power or casting molds.
Description of the Technology
Due to its high melting point, high thermal conductivity and high temperature strength, tungsten is especially attractive when looking for high thermal exhaust and high operational temperature applications. Tungsten, however, is an intrinsic brittle material, especially after recrystallization and grain growth. Brittle materials under load fail by a sudden, unstable propagation of a single crack.
Fiber reinforced materials rely on the additional introduction of fibers with a weak interface to achieve enhanced properties. The major function provided by the fibers is present in the post-cracking zone, in which the fibers interact with the growing crack and activate mechanism which dissipate energy and thus mitigate stress peaks. The composite shows damage tolerance and can bear higher loads compared to the original brittle material. By using this principle, long fiber as well as randomly distributed multi- short fiber Wf/W produced by CVD and powder metallurgical processes with significantly increased mechanical properties have been realized.
Innovation and advantages of the offer
With the incorporation of the tungsten fibers with high strength and ductility, Wf/W can develop so-called pseudo-ductile behaviour. Fracture energy as well as fracture toughness have been significantly increased. For short fibre Wf/W fracture energy has been increased from ~100 J/m2 to more than 1000 J/m2 and fracture toughness from ~5 MPa m0.5 to ~20 MPa m0.5 compared to pure tungsten samples.
Non fusion applications
Based on the developed materials, properties such as ductility, high thermal conductivity and the resistance against wear and erosion makes Wf/W the ideal candidate for high mechanical and thermal stress applications where usual refractory metals are excluded due to their brittleness. This new technology could then find promising applications in areas such as high temperature x-ray cathodes, concentrated solar power, casting molds etc.
EUROfusion Heritage
Materials with high performance regarding thermal properties as well as mechanical properties are required for application in high heat-flux environments, especially in new technologies for advanced energy production (e.g. receivers for concentrated solar power, plasma facing materials in fusion reactors). The Material was developed as Part for the WPMAT project within Eurofusion, previously EFDA as part of the advancement of the divertor high heat-flux component. Here the ability to withstand high thermal loads and resilience against mechanical loads and cracking are superior to use of pure tungsten. The development was started at IPP Garching and is jointly moving on since 2013 between IPP Garching and FZ Jülich